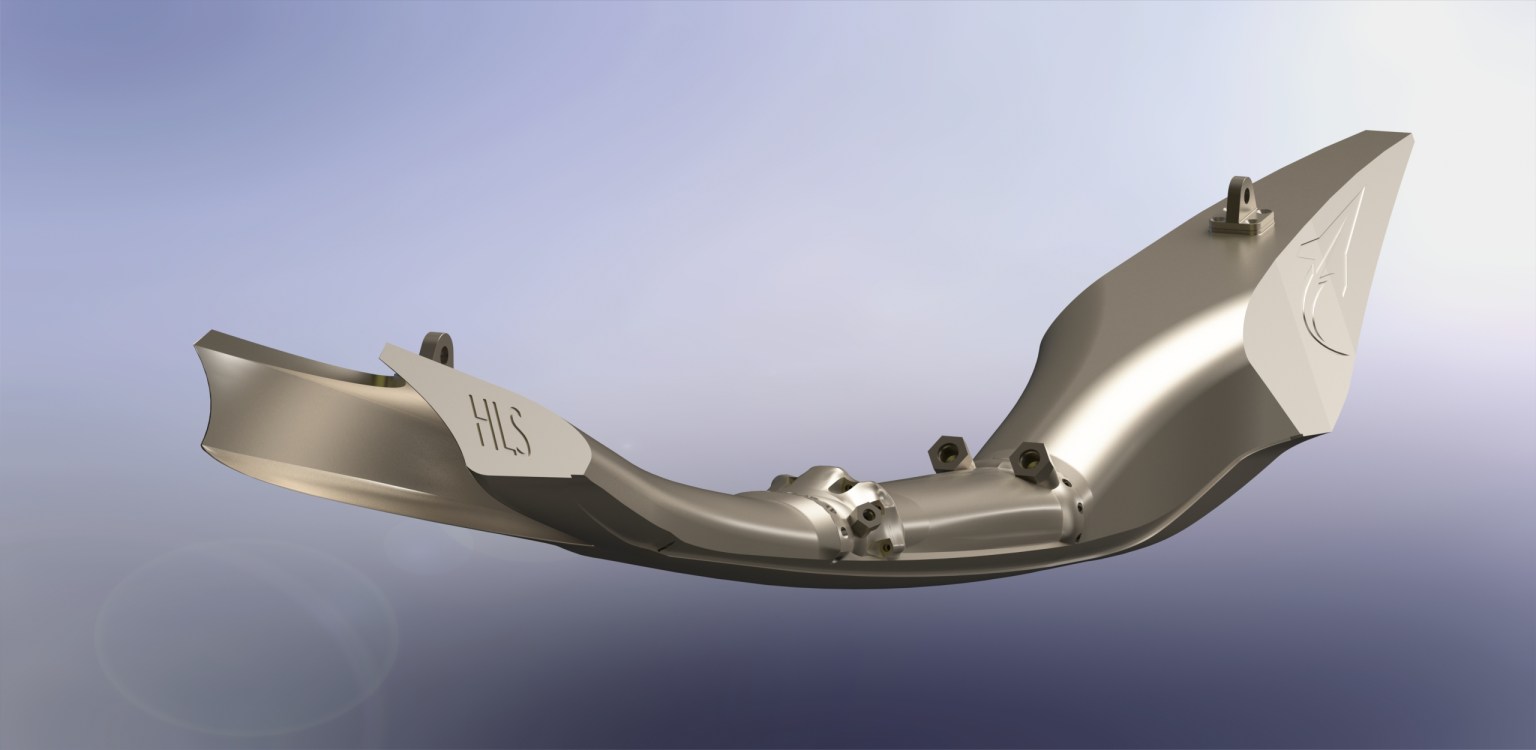
This is proving to be a very busy year for Brisbane-based hypersonic launch system company Hypersonix, with a number of announcements in recent weeks as the company looks to develop its minimum viable product in 2022.
Hypersonix, the company behind the Delta Velos launch vehicle that uses green hydrogen is continuing to build on what has been a very busy year. It is hoped that the uncrewed space launch vehicle, Delta Velos, will reach minimum viable product (MVP) launch by the second half of 2023. The company has recently announced new relationships with global digitalisation company Siemens and Melbourne-based advanced manufacturing company Amiga Engineering, as well as their first international office, based in Germany.
According to Managing Director David Waterhouse, the company is finishing off the year in a very strong position.
“It all came together nicely. We had a fantastic year on many levels. We have developed strong partnerships with industry partners globally, we have opened our office in Europe, we are putting in our first orders and we moved into the build stage during the second half of the year,” he said.
“We feel extremely proud of our achievements but also exhausted, it has been quite the year for the entire team. We have all been working very hard to achieve everything we have in spite of lockdowns and not being able to travel.”
Collaborations with industry
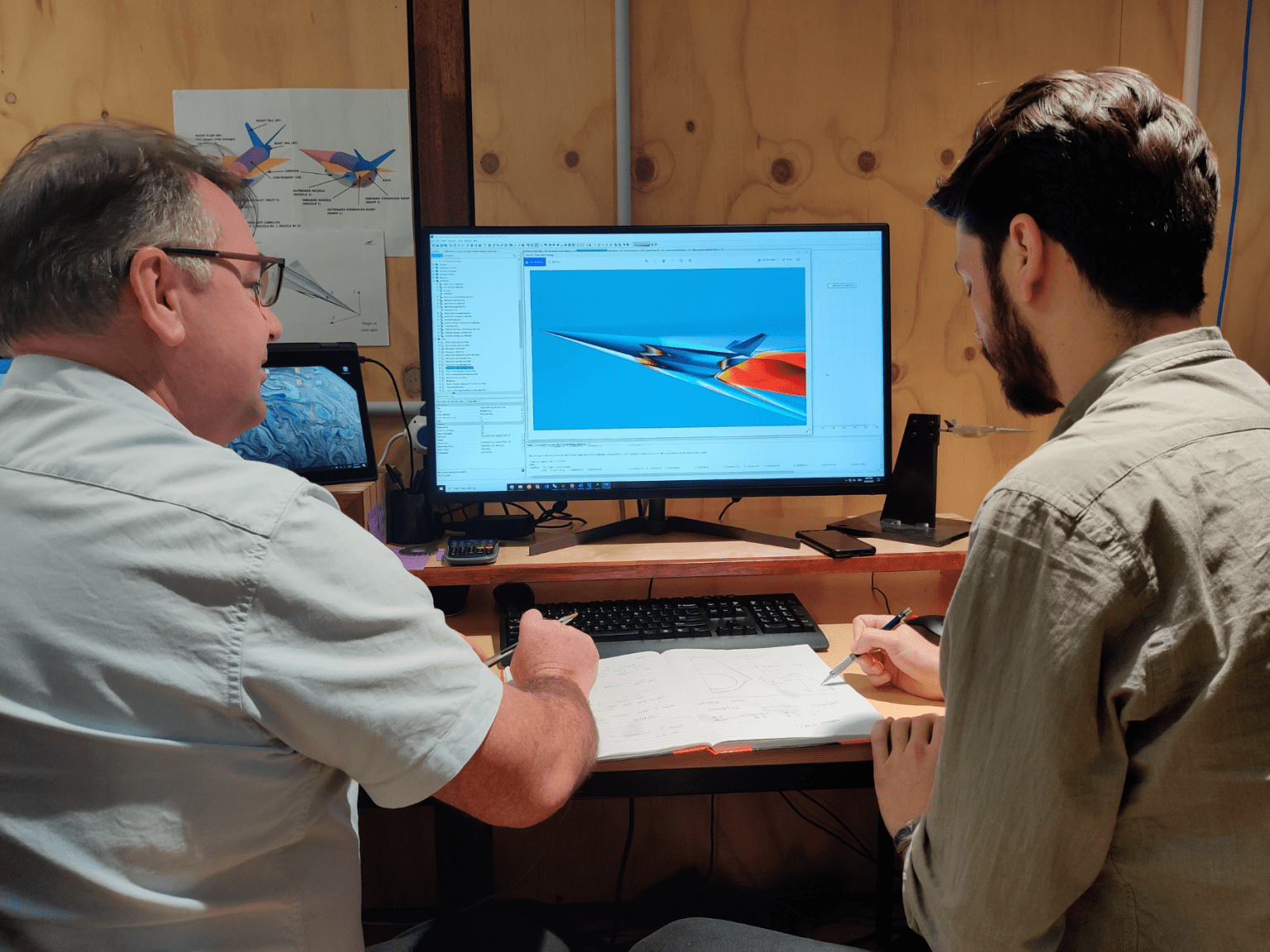
Hypersonix has announced they will be using Siemens Xcelerator portfolio of software to support the design of the Delta Velos launch vehicle. Using the software, which includes the Simcentre STAR-CCM+ program, the company will be able to implement advanced aerodynamic and thermal modelling. This modelling will allow the design team to build certainty and reliability into design development.
This type of advanced computational fluid dynamics (CFD) software allows for the simulation of products under real-world conditions and is widely used in industries where complicated fluid flows need to be understood. This can be anything from how multiphase flows impact engines through to flows within battery cells and of course aerodynamic flows.
Speaking on the announcement, Managing Director David Waterhouse said, “Software has levelled the playing field. We now have the access and ability to not only give sustainable and innovative ideas life using simulation technologies, but also the opportunity to work collaboratively with global companies such as Siemens and tap into their expertise in advanced software for various industries.”
Dr Stephen Hall, who is the Manager Advanced CFD Thermal Structural Simulation at Hypersonix brought in prior experience of the Siemens’ product. Hall first applied Siemens’ Simcenter STAR-CCM+ software to automotive applications when working for the Williams Formula 1 racing team in the UK. His experiences there heavily influenced Hypersonix’ decision to adopt the software.
“The strenuous competitive requirements of Formula 1 demonstrated the ability within Simcenter StarCCM+ to model complex flows around sophisticated vehicle geometries, while performing as a practical tool for rapid design iterations,” said Dr Hall.
Amiga Engineering is also supporting the Delta Velos development with Hypersonix placing an order for the SPARTAN scramjet. The scramjet, which was successfully tested earlier this year, lends itself to Additive Manufacturing, due to its lack of moving parts. The SPARTAN which powers Delta Velos launch vehicle is due for completion in March 2022, after Hypersonix received an Accelerating Commercialisation grant from the federal government in 2020.
“In a demanding industry such as aerospace, additive manufacturing offers the cutting edge in component manufacture capable of creating very complex parts in some of the most exotic materials,” said Michael Bourchier, Founder and Managing Director Amiga Engineering about the project.
“With thousands of hours of research and development in every part, the aerospace industry settles for nothing but the best. We are extremely excited to work with Hypersonix Launch systems on the world’s first 3D printed fixed geometry scramjet engine.”
“The use of Additive Engineering to manufacture a scramjet engine will fundamentally disrupt the cost structure of scramjets and an important step in providing more affordable access to hypersonic flight,” said Waterhouse.
Hypersonix looking at global opportunities
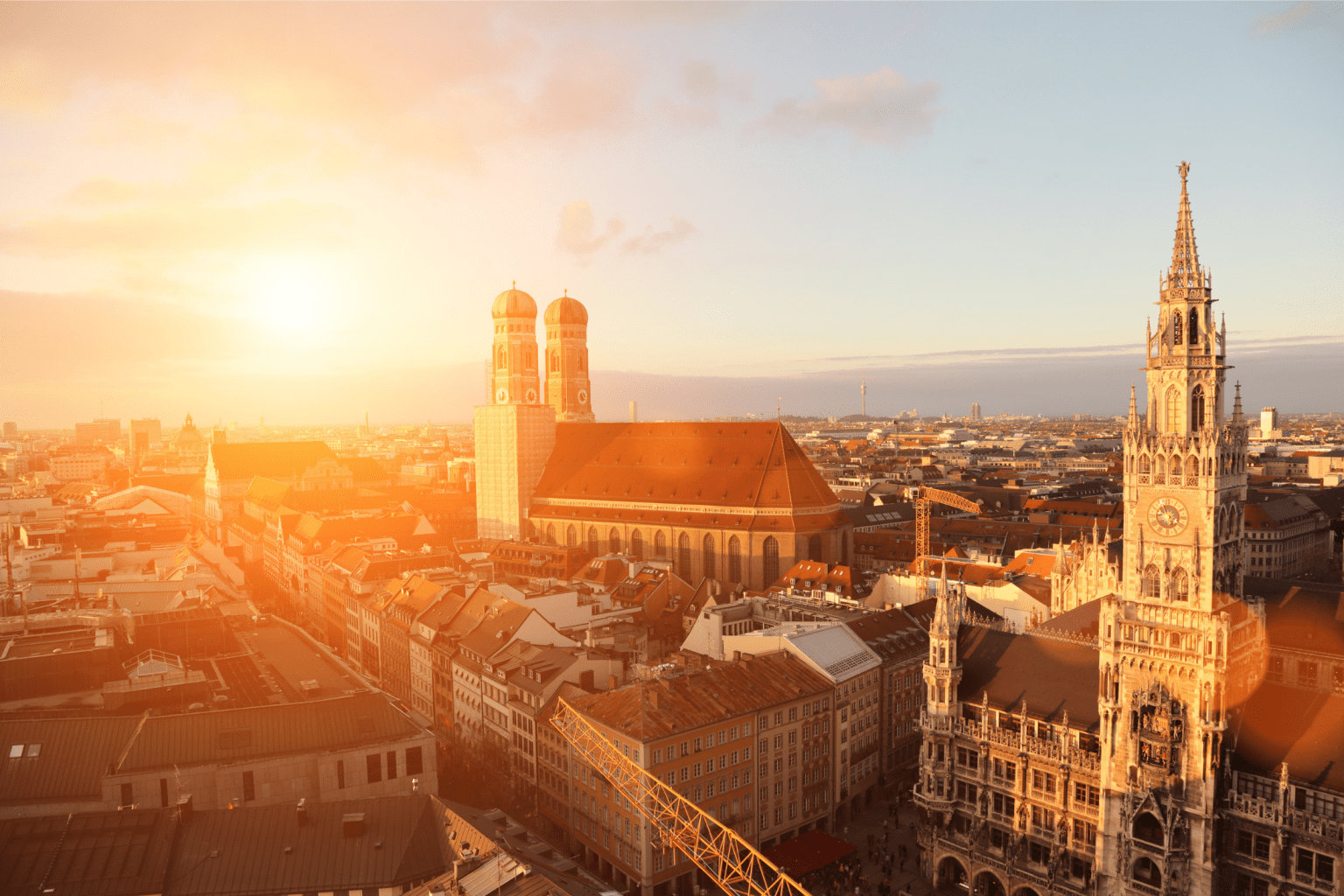
Munich will be the location for Hypersonix’ newest office.
Last month Hypersonix announced they would be opening a new office in Munich, the capital of the German state of Bavaria. This is the company’s first international office and is according to Waterhouse in Germany’s ‘deep tech’ heartland, which will allow Hypersonix to access innovation easier.
The company has already announced it will be working with green hydrogen supplier BOC. BOC’s parent company, Linde Plc was founded in Munich and still has a significant presence there. Germany is also pushing for hydrogen to take a lead role in Germany’s energy transition strategy, releasing a national hydrogen strategy in 2020.
As part of this strategy, the German government announced in October this year that they would provide financial support to projects that support the generation of green hydrogen and its derivatives as well as for storage, transport and integrated uses in the fields of industrial application and experimental development.
“Green hydrogen can deliver thrust five times higher than any other rocket fuel and leaves no CO2 emissions behind, only water vapour,” Mr Waterhouse said.
“We are extremely excited to see our 3D printed scramjet engine soon, having been made in Australia, seeing increased appetite from investors globally and continuing to grow our team. 2022 will be bigger on many levels, watch this space,” he concluded.