Hypersonix and USQ partner to research reusable satellite launch systems
Table of contents
Brisbane-based Hypersonix Launch Systems have entered into a framework agreement with the University of Southern Queensland. The agreement will see the two organisations work together on the Delta Velos reusable launch vehicle.
Hypersonix are continuing to develop their three-stage reusable satellite launch platform and have signed an agreement with the University of Southern Queensland (USQ) to develop the Delta Velos launch vehicle. The project will support the development of high-temperature composites which are an essential technology for the development of Hypersonic vehicles.
Professor Peter Schubel, Director of University of Southern Queensland’s Centre for Future Materials (CFM), said the launch vehicle was a technology demonstrator for key aspects of a re-usable small satellite launch system.
“We are the first university to sign an agreement with Hypersonix Launch System to support their journey towards their first launch approximately two years from now,” added Professor Schubel.
The goal is to investigate materials for their high-temperature resistance and long durability, for the purpose to develop reusable launch vehicles and engines – a game-changer in launch capability. USQ will work with Hypersonix on the design, modelling and prototype build of hypersonic’s vehicle systems using these composites.
“USQ is Australia’s leading high-temperature composites research institution. They also work closely and well with the industry. We believe our collaborative efforts on this program will result in world-leading technology and export opportunities for Australia,” said Hypersonix Managing Director, David Waterhouse.
“The University of Southern Queensland will utilise its extensive testing and analysis suite such as mechanical testing (quasi-static, dynamic and fatigue), thermal analysis and even full-scale thrust pads to determine suitable materials matched to acceptable processing parameters,” said Professor Schubel.
Lifting to orbit using the Delta-Velos
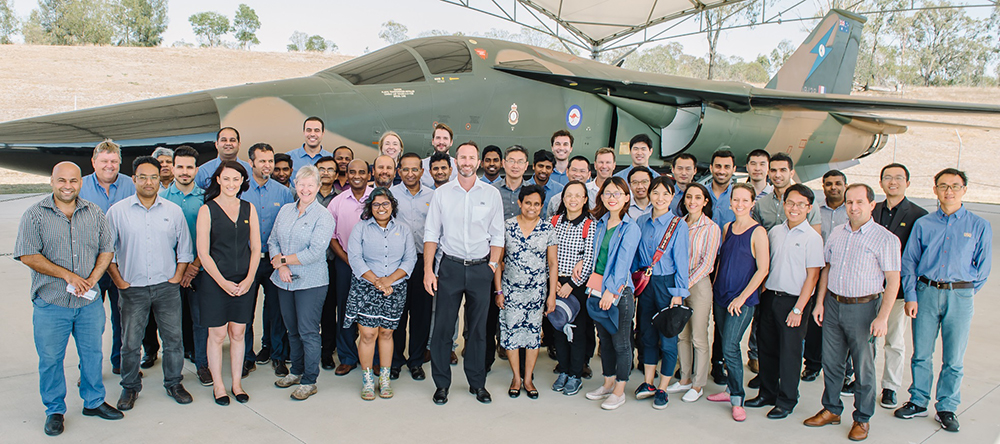
The Delta Velos launch vehicle is part of Hypersonix’s three-stage launch system that will be powered by their reusable scramjet. In May this year, they successfully demonstrated that their scramjet engine can accelerate from Mach 5 to Mach 10.
“We have kicked off the build design of the system. We aim to fly the MVP (Minimum Viable Product) in 24 months. Our relationship with USQ is an important first step along the journey to Australia having a local high-temperature composites build capability,” said Waterhouse.
Material selection has always been a challenge for the Hypersonic’s industry, with the high speeds creating high temperatures and changes in material properties through friction with air molecules during thrust. With new developments in composite materials, reusable hypersonic technology is becoming a reality.
“When travelling at speeds of Mach 5 to Mach 10, the vehicle’s temperature can reach in excess of 1800-degree Celsius. At this temperature, normal metal alloys would melt and carbon composites turn to dust. USQ is doing leading research of HT CMCs and SiC/SiC composites that are both heat resistant and lightweight, making them ideal for aerospace applications,” said Waterhouse.
High-Temperature Ceramic Matrix Composites (or HT CMCs) provide the necessary material properties for hypersonic flight, which is more than five times the speed of sound in air.
A number of materials have been used in hypersonic vehicles over the years including a high-strength nickel alloy named Inconel X that was used on the X-15 NASA test aircraft, which was the first piloted hypersonic aircraft.
However, these materials, particularly for reusable vehicles, need to withstand varying aerodynamic loads, high-speed impacts from weather, such as rain, and be damage tolerant, as well as manage the thermal challenges. HT CMCs are seen as the future as they can mitigate these challenges, are relatively lightweight, and can be manufactured into complex shapes.
This is exactly what excites the team at USQ.
“An element of this development is the challenge around heat management and materials that can operate in highly challenging and harsh environments such as 800-degree Celsius surface temperatures of the Delta Velos vehicle caused by air friction at hypersonic speeds,” said Professor Schubel.
Developing understanding and manufacturing processes for these exotic materials allows efficient vehicle design and effective construction, training of personnel; ultimately providing sovereign capability.”
“Much of the initial modelling work will be done using Hypersonix flight modelling software. This allows us to predict the temperatures on the vehicle and the loads. This is particularly true of the vehicle leading edges and combustion chamber. When we have finalised our materials selection, we will build a prototype MVP and fly it,” added Waterhouse.
A busy year for Hypersonix
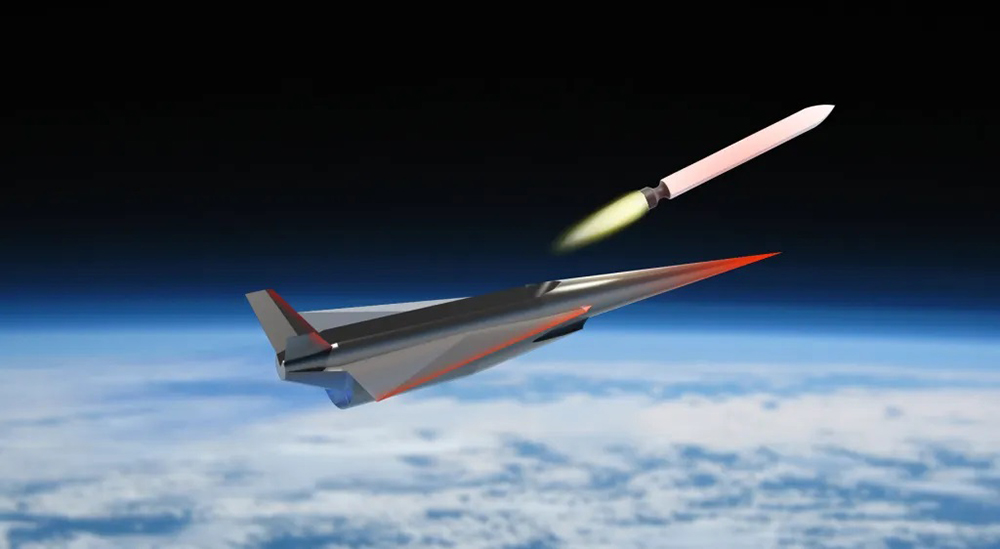
Hypersonix are having a very buoyant 2021 with the company collaborating with a number of organisations to develop their hypersonic vehicles. In August of this year, Hypersonix signed an agreement with PFI Aerospace to support the manufacturing of the Delta Velos launch vehicle. They also signed an agreement with Romar in July to investigate advanced manufacturing techniques to support the development of the launch vehicle.
According to Waterhouse, “High-temperature composites are a fast-evolving technology with high demand in the Transport Industry and particularly the Aerospace Sector. At Hypersonix our aim is to facilitate an Australian sovereign build capability in the Aerospace sector. In this high-temperature composites area, Australia is ‘playing catch-up’ with North America and Europe, and we are probably 5 years behind the best in breed manufacturers today.”
The principle of “green space” is important to Hypersonix, with reusability being a major priority for the development of their launch vehicle and earlier this year they partnered with BOC to use green hydrogen as a fuel for their system.
“The University of Southern Queensland and Hypersonix have like-minded goals in that they wish to push the boundaries of space exploration by developing sustainable launch vehicles that will service an ever-increasing Space economy,” concluded Professor Schubel.
Written by Ruth Harrison